
A byproduct of this chemical reaction is CO2. Towering blast furnaces heated to above 1,000C are loaded with the mineral, lime and coke, a fuel derived from metallurgical coal that removes the oxygen molecules from iron oxide. The reason why steel is so carbon-intensive comes down to the principal route for extracting iron from its ore. It is not cheap, and our customers should be ready to pay,” says executive chairman Lakshmi Mittal.Īt its Ghent plant in Belgium, ArcelorMittal is building a facility that will convert toxic waste wood into ‘bio-coal’, with a lower CO2 footprint than traditional processes © Francois Lenoir/Reuters Decarbonising targets “These technologies will increase the cost of our steel. Among the obstacles is the level of investment required, which could run into hundreds of billions of dollars - not easy in a business plagued by chronic oversupply and volatile swings in profitability.ĪrcelorMittal, Europe’s biggest steelmaker, has estimated that decarbonising its facilities on the continent in line with the EU’s drive to eliminate net greenhouse gas emissions by 2050 will cost between €15bn and €40bn. However, overhauling a monolithic and slow-moving smokestack industry that churns out 2bn tonnes a year of product will be an enormous task.
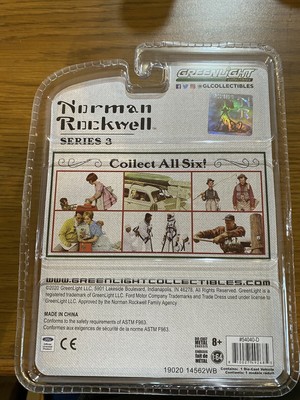
The most ambitious plans involve moving away from a principle for turning rock into metal discovered in the iron age, with “clean” hydrogen gas as a new alternative energy source. “We’re still not yet at the point of market readiness, but it’s progressing relatively fast and we can expect a first wave of close-to-zero production sites before 2030.” It says this will result in virtually no CO2 emissions © SSABįaustine Delasalle, a partner at Systemiq, a sustainability consulting and investment company, says the level of technical development is encouraging. To meet global climate and energy goals, steel industry emissions must fall by at least half by the middle of the century, according to the International Energy Agency, with declines to zero pursued thereafter.Īt a pilot plant in Lulea, Sweden, SSAB will soon begin trials using hydrogen gas to reduce iron ore. Breakthrough technologies are needed urgently.”Īfter the mass deployment of renewable energy over the past decade, as well as recent pledges by many of the world’s automakers to switch to electric motors, heavy industries such as steel, cement and petrochemicals that require extreme heat are one of the next frontiers in the decarbonisation of the economy. “If we really want to contribute to realising the climate goals set in the Paris agreement, then there’s a quite widespread consensus that only doing further efficiency improvements in the blast furnace will not be enough. It has been made since a long time back from iron ore, using coal,” says Martin Pei, chief technical officer at SSAB, a Swedish company at the forefront of these efforts.

“Steel is a very important material for modern society. German industrial conglomerate Thyssenkrupp is one of a number of companies to have announced targets for so-called ‘net zero’ emissions © Ina Fassbender/AFP/Getty
